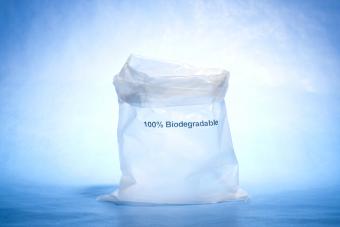
Biodegradable plastics can be biobased or fossil fuel based. New types of plastics have been produced in recent years to address the plastic pollution problem, by trying to shorten the time needed to degrade them, especially in natural conditions. However, not all the current biodegradable plastics have achieved this aim.
Definition of Biodegradable Plastics
Biodegradable plastics are those that can be degraded by microbial action to produce natural end products, like water and carbon dioxide, in a reasonable period of time. The time needed to decompose completely depends on the material, environmental conditions such as temperature and moisture, and location of decomposition according to Biodegradable Products Institute (BPI pg. 2).
Compostable plastics are those that biodegrade rapidly and turn into humus that is not contaminated by metals. Not all biodegradable plastics are compostable; only some are.
Materials must meet ASTM Specifications D6400 or D6868 to be called biodegradable and compostable on land, and meet ASTM D7081 specifications for marine environments. ASTM is a worldwide product standards group.
Biobased Polyster Plastics That Biodegrade
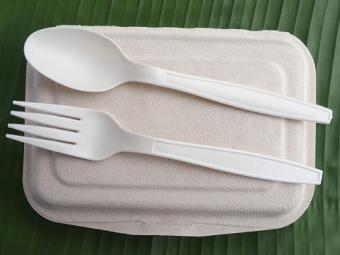
Plastics that are derived from plants are called biobased plastics. Not all of these are biodegradable; for example there are biobased PET bottles made to be durable. The biobased plastics that biodegrade are made of two materials: biomass and polysters derived from plants. There are two kinds of biobased polysters: polylactide acid (PLA) and polyhydroxyalkanoate (PHA).
Polyhydroxyalkanoate (PHA)
PHA is produced naturally by bacteria and Genetically Modified Organisms (GMO) plants, but there are plans to try production from food waste. Polyhydroxybutyrate or PHB is also a kind of PHA that is widely used. PHAs are expensive to make as only limited quantities can be produced from bacteria.
- Uses: PHAs are used as food wraps, cups, plates, coating for paper and cardboard, and 'many medical uses, including sutures, gauzes, and coatings for medicines' according to a report by the Centre for Industry and Education Collaboration (CIEC report). It can replace most of the major fossil fuel based plastic types currently used, such as PE, PS, PVC, and PET points out Bio Based Press.
- PHA-blended starch/cellulose plastics: Some plastic items are made entirely of PHA, as in case of water bottles notes Bio Based Press. However, since production of PHA is expensive, it is also blended with starch and cellulose to make it more economical. This has the added advantage of improving the rate of decomposition according to the Dartmouth Undergraduate Journal of Science (DUJS).
- Biodegradation: It can be completely compostable in environments that are rich in microbes and fungi, especially soil. These microbes breakdown the PHA with the help of enzymes. The time necessary to degrade depends on the concentration of microbes in the environment.
- PHA takes two months to decompose in backyards, according to Bio Based Press.
- The rate of decomposition is much slower in marine waters where less than 50% is broken down after six months adds CalRecycle (pg. 6). PHA passed the ASTM D7081 test by showing 30% decomposition in six months (pg. 7).
Polylactide Acid (PLA)
The DUJS explains that PLA is a thermoplastic made through fermentation by bacteria. PLA are actually a long chain of many lactic acid molecules. Since there are many inexpensive means of producing lactic acid, these have only to be polymerized or joined. Therefore, PLA is less expensive than PHA. However, PLA is brittle and its application is more restricted than PHA. Manufacturers get around this problem by including additives or polymers.
- Uses: It is made into grocery bags, food packaging, bottles, cups, and plates. Since it decomposes well in the presence of acids, it is used in some medical applications like medical sutures and plates, where it dissolves after 90 days notes the CIEC report. It is also used in 3-D printing of objects.
- PLA and polymer blends: PHA can also be blended with polymers from renewable sources to improve its qualities according to DUJS.
- Biodegradation: PLA cannot be composted easily in the backyard because temperature and water levels needed are not available in this environment.
- PLA can take six-12 months to degrade in soil.
- PLA takes three-six months to degrade in commercial facilities, notes World Centric.
- When decomposition happens in the presence of oxygen, the end products are carbon dioxide and water.
- If PLA degradation occurs in landfills without oxygen, it produces methane gas that is 20 times more detrimental to the environment than carbon dioxide points outan American Chemical Society release (pg. 2).
- PLA did not pass the ASTM D7081 test as only 3% decomposed in marine waters after six months according to CalRecycle (pg. 7).
Since PLA does not decompose quickly in soil or seawater, this can become a problem when littered.
Biomass Based Biodegradable Plastics
Biomass based plastics are made of starch and cellulose obtained from crop residues as well as wood from trees.
Cellulose Acetate
Cellulose acetate (CA) is a synthetic product that is derived from cellulose that is found in each part of a plant. Cellulose is currently used from cotton, wood, and crop waste according to a 2018 scientific publication. This can be used to form molded solid plastics, cigarette filters, coatings, photographic-films and filters. Cellophane is a biodegradable film produced from cellulose. There is ongoing new research to find new plastic films from waste crop and wood material that are water resistant and biodegradable according to Phys.org.
- Biodegradability: Research shows that CA degrades and is reduced by 70% of its weight after 18 months in nature.
Starch
A 2017 review notes starch is treated with heat, water, and plasticiers to produce a thermoplastic. To improve its strength, it is combined with fillers made of other materials. The main sources of starch are maize, wheat, potato, and cassava. This plastic is used in packaging, bags, and agricultural mulch films, tableware, flower pots, and molded to make packaging and consumer goods. It is seen as an alternative for polystyrene (PS) according to Food Packaging Forum. Starch is added to biobased and conventional plastics to make them more biodegradable notes a 2017 Phys report.
- Biodegradability: Starch-based plastics can be compostable or only biodegradable. Compostable variants require 90 days to degrade in industrial facilities, while the biodegradable ones require 100 days for 46% to degrade and up to two years to degrade completely.
Fossil Fuel Based Biodegradable Plastics

According to Bioplastics Guide, there are a few new fossil fuel plastics that can also be biodegradable. The most common ones are Polybutylene succinate (PBS), Polycaprolactone (PCL), Polybutyrate adipate terephthalate (PBAT) and Polyvinyl alcohol (PVOH/PVA).
- PBAT is a polymer that is produced from fossil fuel derivatives and is used sometimes in combination with starch. Efforts are on to produce this polymer from renewable sources. Bioplastics guide see it as a substitute for LDPE and HDPE. It is used to make garbage bags, wrapping films, disposable packaging and tableware (cups, dishes etc.). It is not only biodegradable but also compostable.
- PCL is a synthetic polyster used to make compostable bags, in medical application (sutures and fibers), as surface coatings, adhesives for shoes and leather, and stiffeners for shoes and orthopaedic splints. This plastic can be decomposed by yeasts. More than 90% of films, and 40% of foam made of this material can be degraded in 15 days.
- PBS is a resin produced from fossil fuels or can also be biobased according to Succinity (pg. 1, 5). It can be combined with other biobased polymers or fibers like jute to improve its quality. PBS is used to make food packaging, service ware, agricultural mulch sheets, plant pots, hygiene products like diapers, and fishing nets.
- PVOH is a resin that can be used to make packaging films that can replace LDPE and HDPE. Its other important applications are as coatings and additives for paper and board production according to Food Packaging Forum.
All four fossil fuel based plastics biodegrade in three months in industrial composting, in one year in backyard composting and in one to two years in soil/ landfills according to InnProBio (pg. 4).
Recycling and Composting
Properties of the different biodegradable plastics must be kept in mind to treat them at the end of their life-cycle, cautions the Environmental Protection Agency (EPA).
- EPA explains that biodegradable plastics should not be added to bins which recycle conventional plastics as they are made of different materials. This is true for both the biobased and the fossil fuel types.
- Even though plastics are marked as biodegradable and compostable, many of them can degrade only in conditions available at commercial composting facilities; contact local recycling agencies for information on the nearest compost plant. There were only 200 such facilities in the U.S. in 2017, so these kinds of centers need to be increased.
- Confirm that bags are compostable at home by following product instructions before adding them to the compost bins.
- Recovery of material from biodegradable plastics is not possible through recycling, due to lack of facilities.
Efficient segregation, collection, and degradation is necessary to take advantage of the biobased and biodegradable plastics. In its absence, most of the biodegradable plastics end up in landfills.
Future of Biodegradable Plastics
The biodegradable nature of plastics cannot solve the problem of plastic pollution if they are not properly disposed. It is also still necessary for consumer behaviour to stay focused on reducing consumption or recycling plastic to benefit from the change from conventional fossil fuel plastics to biodegradable plastics.